EPS SHAPE MOLDING MACHINE
About EPS moulding machine
The eps shape moulding machine made by YANTAI DMENG MACHINERY CO., LTD, also known as the EPS shape molding or EPS block molding machine, is a specialized piece of equipment used in the manufacturing process of Expanded Polystyrene (EPS) foam products. EPS foam is a lightweight and versatile material widely used in packaging, construction, and various other applications due to its excellent insulating properties and structural integrity.
Table of Contents
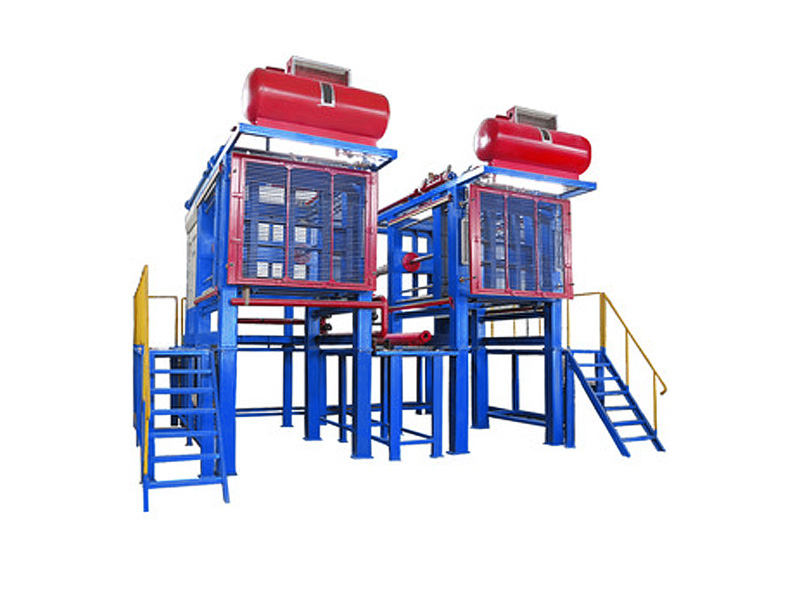
The units of eps shaper moulding machine units
- Pre-Expander Unit: This part is responsible for the pre-expansion process, where raw EPS beads are exposed to steam, expanding them and making them suitable for molding.
- Aging Silos: After pre-expansion, the pre-expanded EPS beads are stored in silos, allowing for proper aging and stabilizing the beads’ size and properties.
- Molding Chamber: The molding chamber or mold cavity is where the pre-expanded EPS beads are placed to take on the desired shape and size of the final foam product. The mold is usually made of aluminum and can be customized for different product designs.
- Steam Injection System: Steam is injected into the molding chamber, causing the pre-expanded beads to further expand and fuse together to fill the mold’s cavity.
- Cooling System: After the steam molding process, a cooling system is used to cool down the molded EPS foam, solidifying it in the desired shape.
- Ejector System: Once the cooling is complete, the ejector system helps to remove the molded foam product from the mold, preparing the machine for the next cycle.
- Hydraulic System: EPS molding machines may utilize a hydraulic system to control the movements of the mold and other mechanical parts involved in the molding process.
- Control Panel: The control panel is the interface that allows operators to control and monitor the machine’s functions. It includes various settings, timers, and temperature controls.
- Feeding System: This system is responsible for transferring the pre-expanded EPS beads from the aging silos to the molding chamber efficiently.
- Safety Features: EPS molding machines include safety features such as emergency stop buttons, safety guards, and sensors to ensure safe operation and protect operators from potential hazards.
How to shape EPS foam products?
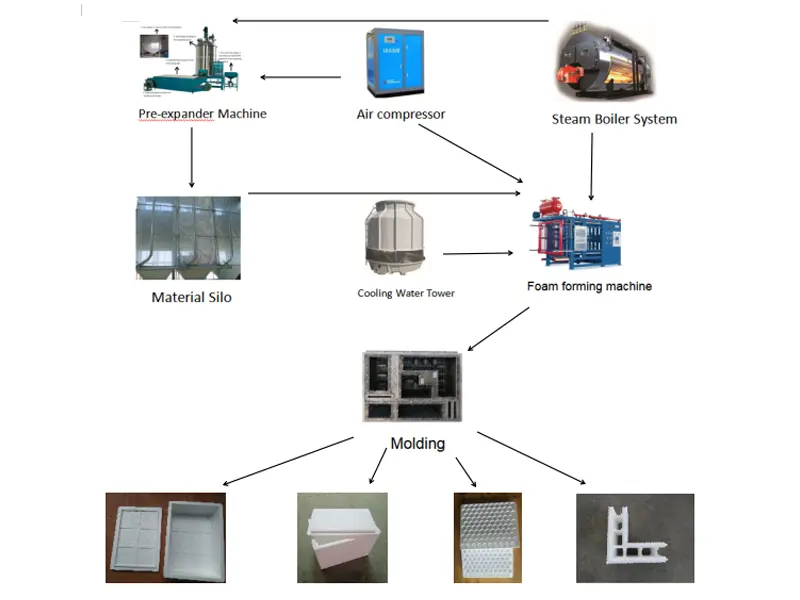
- Pre-expansion: Raw EPS beads are pre-expanded using steam to increase their size and reduce their density. This pre-expansion makes the beads easier to mold and helps to achieve the desired properties of the final EPS foam product.
- Aging: The pre-expanded EPS beads are left to age for a specific time to allow any residual pentane (blowing agent) to evaporate completely. Aging ensures the stability and consistency of the beads.
- Molding: The pre-expanded EPS beads are poured into a mold cavity within the EPS shape molding machine. The mold is then closed, and steam is injected into the beads, causing them to expand and fuse together, taking the shape of the mold.
- Cooling: After molding, the steam is released, and the mold is cooled using air or water to solidify the EPS foam and retain the molded shape.
- Ejecting: The molded EPS foam product is ejected from the mold, and the process is ready for the next cycle.
The usage of eps foam products
- Packaging: EPS foam is extensively used in packaging materials for fragile and delicate items such as electronics, appliances, glassware, and other sensitive products. EPS foam provides excellent cushioning and protection during transportation and storage.
- Construction: EPS foam is used in the construction industry for insulation, both in residential and commercial buildings. It is used as an insulating material in walls, roofs, floors, and foundations, helping to regulate indoor temperatures and improve energy efficiency.
- Packaging Inserts: EPS foam is often used as packaging inserts to securely hold and protect items inside shipping boxes. It is commonly seen in products like electronics, furniture, and appliances.
- Coolers and Insulated Containers: EPS foam is used in the production of coolers and insulated containers, which are widely used for transporting perishable goods, pharmaceuticals, and temperature-sensitive products.
- Food and Beverage Packaging: EPS foam is used for food and beverage packaging, such as takeaway food containers, cups, and trays. It helps in keeping food items hot or cold and provides excellent insulation.
- Flotation Devices: EPS foam is used in the manufacturing of flotation devices like life jackets, life buoys, and floating rafts due to its buoyant properties.
- Arts and Crafts: EPS foam is used in various arts and crafts projects, including model building, sculpting, and DIY projects due to its ease of cutting and shaping.
- Medical and Healthcare: EPS foam is used for protective packaging in the medical industry for transporting delicate medical equipment and devices.
- Theater and Movie Props: EPS foam is used in theater and movie productions to create props and set designs due to its lightweight and easily sculptable nature.
- Soundproofing: EPS foam is used in soundproofing applications to reduce noise and vibrations in rooms and studios.
- Geofoam: EPS foam is used as a lightweight fill material in civil engineering and construction projects, such as road embankments, bridge approaches, and landscape modifications.
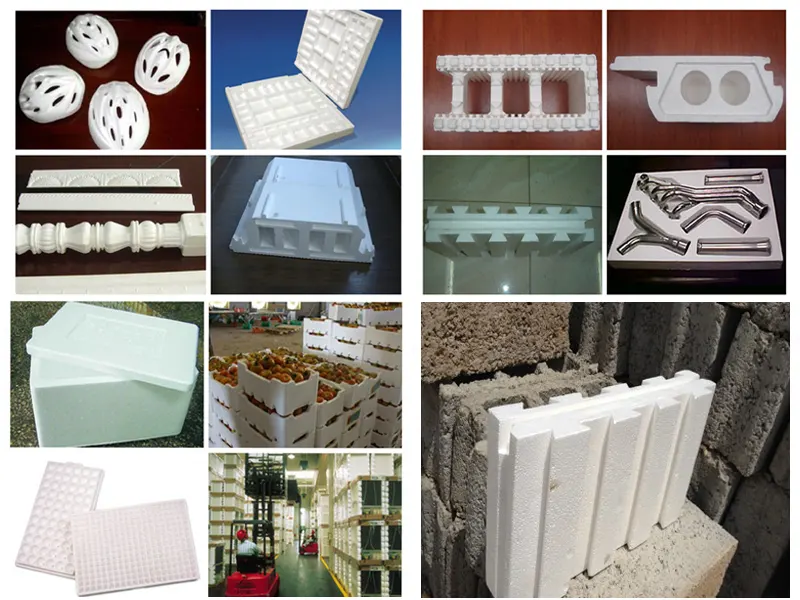
How to choose eps molding machine?
- Production Capacity: Determine your required production capacity in terms of the number and size of EPS foam products you need to produce per hour or per day. Choose a machine that matches your production requirements and can meet your production targets efficiently.
- Product Size and Shape: Consider the size and shape of the EPS foam products you intend to manufacture. Ensure that the machine you choose can accommodate the desired product dimensions and mold configurations.
- Automation Level: Decide on the level of automation you need based on your production volume and available labor. EPS molding machines come in manual, semi-automatic, and fully automatic configurations. Automated machines increase productivity and reduce labor costs.
- Energy Efficiency: Look for an EPS molding machine that is energy-efficient. Energy-efficient machines can help you save on operational costs and contribute to environmental sustainability.
- The following is our series of foam pipe machine for your reference
- Set a budget for your EPS molding machine purchase and compare the features, specifications, and prices of different machines within your budget range.
ITEM | DY-1200 | DY-1400 | DY-1600 | DY-1750 | |
Mould Dimension(mm) | 1200*1000mm | 1400*1200mm | 1600*1400mm | 1750*1450mm | |
Max Produce Size(mm) | 1050*850*400 | 1250*1050*400 | 1450*1250*400 | 1600*1300*400 | |
Stoke(mm) | 150-1350 | 150-1350 | 150-1350 | 150-1350 | |
Steam | Entry | DN80 | DN80 | DN100 | DN100 |
Consumption | 5~7kg/cycle | 6~9kg/cycle | 7~10kg/cycle | 8~12kg/cycle | |
Pressure | 0.5~0.7Mpa | 0.5~0.7Mpa | 0.5~0.7Mpa | 0.5~0.7Mpa | |
Water | Entry | DN80 | DN80 | DN80 | DN80 |
Consumption | 45~130kg/cycle | 50~150kg/cycle | 55~170kg/cycle | 55~180kg/cycle | |
Pressure | 0.3~0.5Mpa | 0.3~0.5Mpa | 0.3~0.5Mpa | 0.3~0.5Mpa | |
Air | Entry | DN50 | DN50 | DN50 | DN50 |
Consumption | 1.5m3/cycle | 1.8m3/cycle | 2m3/cycle | 2.5m3/cycle | |
Pressure | 0.5~0.7Mpa | 0.5~0.7Mpa | 0.5~0.7Mpa | 0.5~0.7Mpa | |
Vacuum motor | 5.5kw | 5.5kw | 7.5kw | 7.5kw | |
Hydraulic motor | 5.5kw | 5.5kw | 7.5kw | 7.5kw | |
Cycle time | 60~100s | 60~120s | 70~140s | 70~140s | |
Power | 13kw | 13kw | 17kw | 17kw | |
Machine overall size(mm) | 5200*2200*4500 | 5300*2300*4600 | 5400*2400*4700 | 5400*2600*4800 | |
Weight | 5100kg | 6400kg | 7600kg | 8100kg | |
Other Size Can Also Be Made According to Client’s Requirements |